COMPANY INSIGHT
Sponsored by NHP Electrical Engineering Products
NHP - Enabling the Connected Enterprise
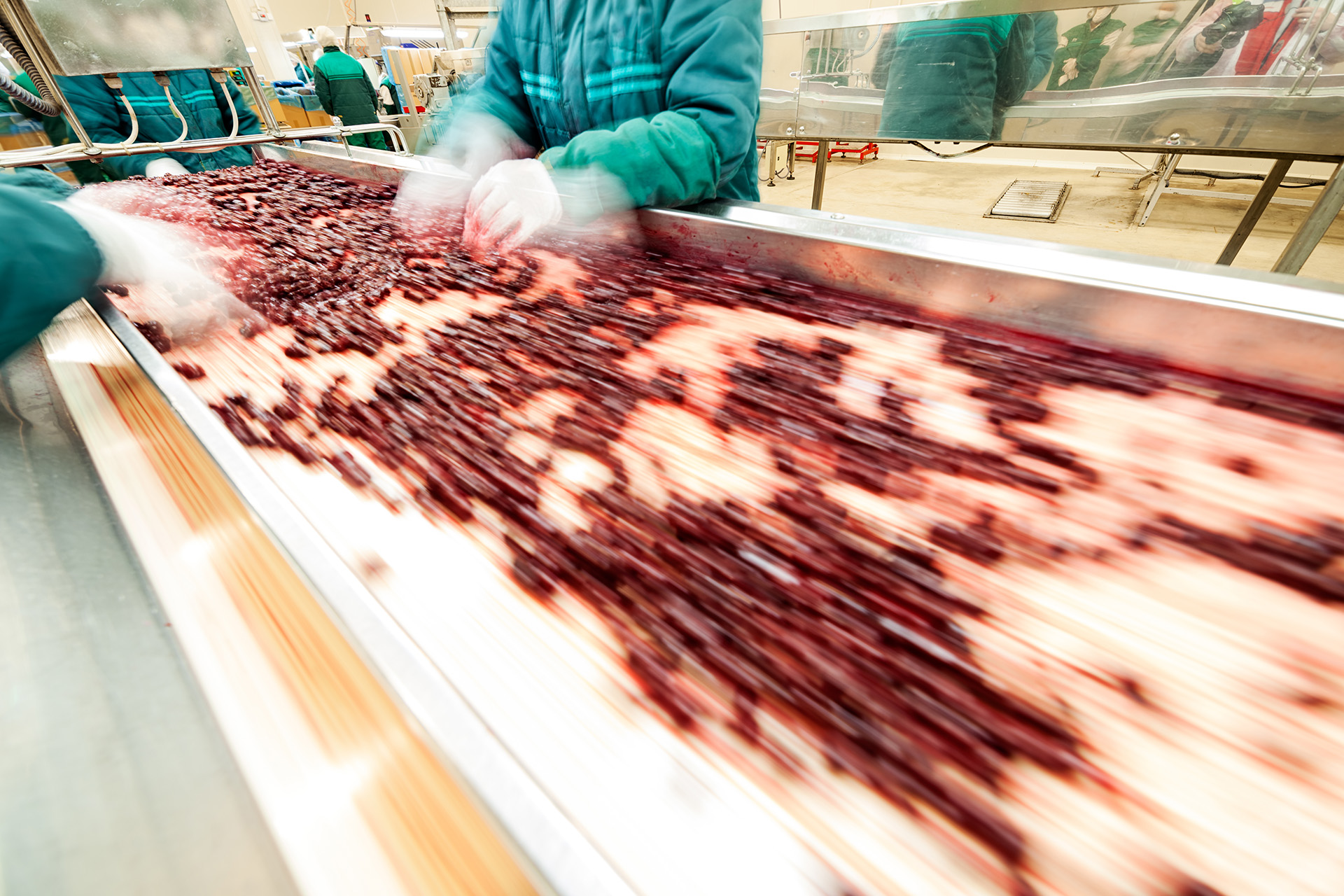
W
ith more than 50 years of electrical and engineering industry excellence and over 20 branches across Australia and New Zealand, it is NHP’s local people and footprint that helps us to understand your specific project needs, no matter how big or small.
As the exclusive distributor for Rockwell Automation throughout the South Pacific region, NHP has been assisting customers to achieve better visibility into processes, data and analytics. Through our SMART digital devices, we have helped thousands of customers on their journey to digitally transforming their operations by assisting them to enable the Connected Enterprise.
Three things define our business: independence, service and advancement. NHP remains independent in order to provide multiple brands and maximum choice for Australasian industrial conditions. We pride ourselves on going the extra mile to support our customers with technical expertise and after sales support.
While we go to market with over 15,000 stocked items, we are much more than a product supplier. Together with our extensive network of global partners, we offer choice in product, choice in technology, choice in service, choice in support and ultimately choice in how you deal with us - whether that be in person or online, where and when you need us.
When it comes to finding a local partner with a global network for your next project, choosing NHP will unlock a world of expertise across electrical and automation products, systems and solutions.
NHP Services
The NHP Service Team – offering so much more than quality electrical and automation products
In conjunction with our major supply line partners, NHP offers our customers services and training solutions, leveraging industry and technology-specific expertise, to maximise operational investments, improve your business and meet your everyday needs.
Technical training
With over 500 technical training courses, seminars, workshops and webinars held annually for the Australian and New Zealand markets, NHP can help to improve your knowledge in the areas of Automation and Process Control, Hazardous Area, Safety Standards, Drives, Vibration, PLC Software, Enclosures, Comptuterised Maintenance Management Systems and much more.
On-site support
NHP, backed by Rockwell Automation, offers a range of on-site field service solutions to suit a wide range of needs. Whether your need is for installation and commissioning, migration, emergency breakdown or lifecycle services, NHP has engineers and technicians placed in strategic locations throughout Australia and New Zealand to respond to your needs.
Repair and remanufacture
Are you confident that your spare parts will operate correctly when needed? NHP takes pride in our repair and remanufacture capabilities. Our repair technicians or supply partners will repair or remanufacture your equipment, using replacement parts that meet or exceed the original design specifications.
Simple, flexible and worry free service agreements
NHP offers a range of tailor made service agreements, from spare parts management, on-site and phone support, repairs and preventative maintenance.
If you have any enquiries relating to NHP Services or would like to schedule in a service, please send an email to nhpservice@nhp.com.au
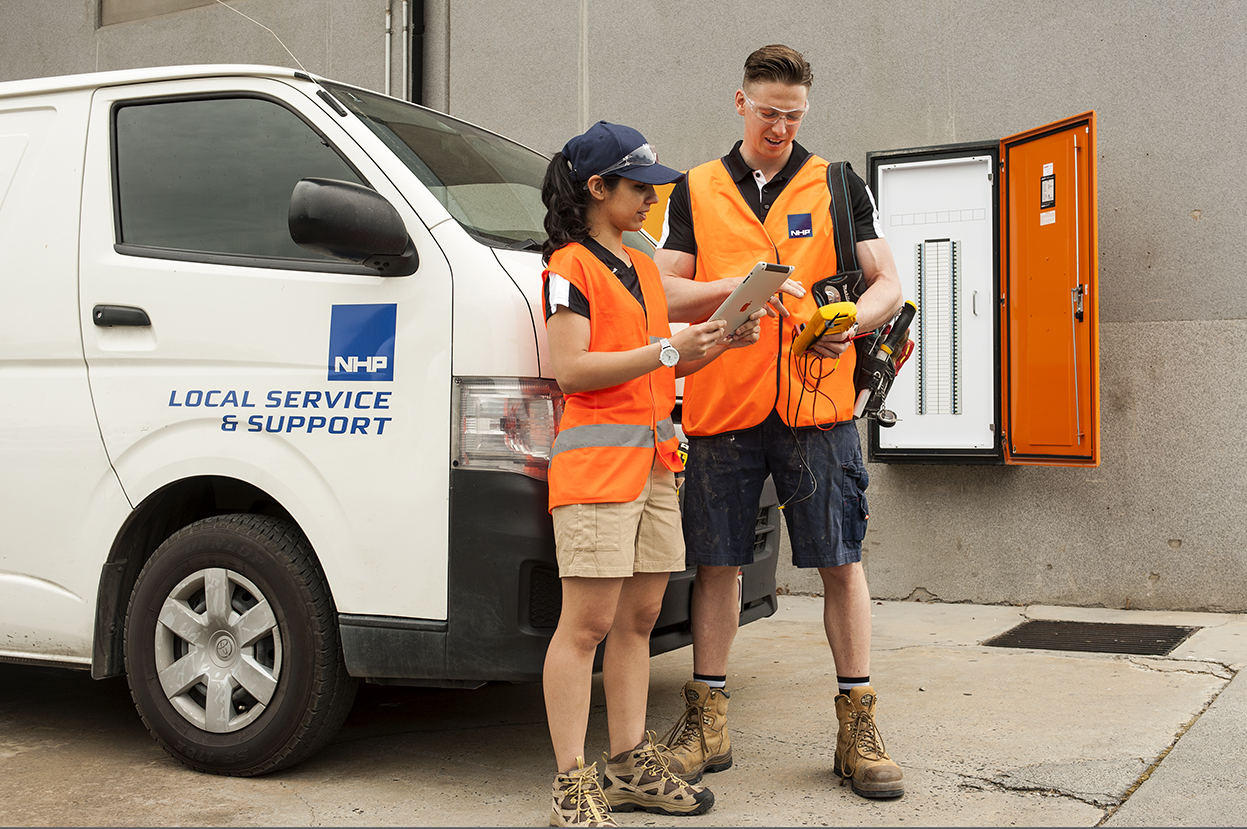
The journey to SMART Manufacturing - Modernising systems to enable the Connected Enterprise
As operations move to ‘smart’ manufacturing, everyone from operators and technicians to corporate executives are using smart capabilities to gain new efficiencies, improve product quality and make operations more responsive. Industrial operators are modernising aspects of their processes and plants, converging Information Technology (IT) and Operations Technology (OT) functions to be more productive in an increasingly competitive global environment. Together, NHP and Rockwell Automation achieve this through The Connected Enterprise.
As a result, operations are becoming faster, more innovative, and more reliant on integrated machinery and equipment to increase throughput and production flexibility. While working to enable The Connected Enterprise and with downtime costs on the rise, manufacturers have to figure out how to get the most out of their aging infrastructure. They are challenged with finding support for ongoing maintenance needs, greater complexity in spare parts management and an increased risk of losing vital expertise.
Working with NHP and Rockwell Automation will help you stay ahead of maintenance issues, so you can minimise the risk of downtime as you modernise.
Click below to access a whitepaper which will investigate:
- why we need to modernise and why the time to do it is now
- what needs to be done and how?
- who needs to take action?
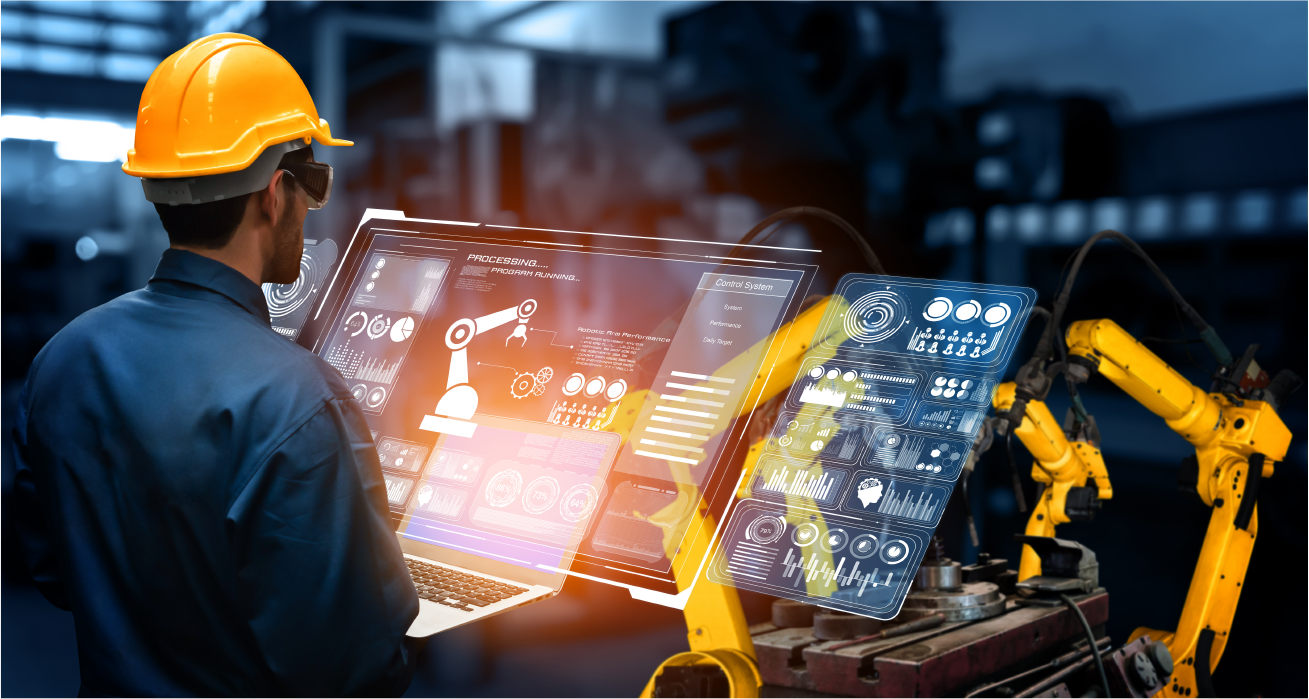
Live circuit warning indicators save lives!
REMLIVE electrical safety live line indicators have been keeping workplaces in Australia safe for more than a decade. The live line or positive isolation indicator (RL24IC) provides a visual reminder that a circuit is live, which reduces the risk of accidents, protects assets, speeds up the fault-finding process and ultimately saves lives.
The primary function of a REMLIVE live line or positive isolation indicator is to provide visual confirmation of correct isolation. The REMLIVE product is connected to the outgoing side of the isolation point and between the load so that the user performing the isolation check can view the positive change of state after isolation. This is important, as even after isolation has occurred, hazardous voltage levels can still be present due to stored energy feedback - the REMLIVE live line indicator provides visual confirmation of this.
It is important to note that other safety isolation and testing procedures still apply before interfacing with the switchboard and control panel.
The REMLIVE live line indicator is supplied with three major components - a DIN rail mount main panel unit, a door display mount unit and a RJ45 cable to connect the main panel unit with the door display. The main panel unit is simply mounted to DIN rail - typically inside the switchboard or control panel assembly - and is connected at the load side of the isolating switch. The panel unit connects directly to the door mount display unit via a RJ45 cable, and both the main panel and door display unit are electrically isolated from one another.
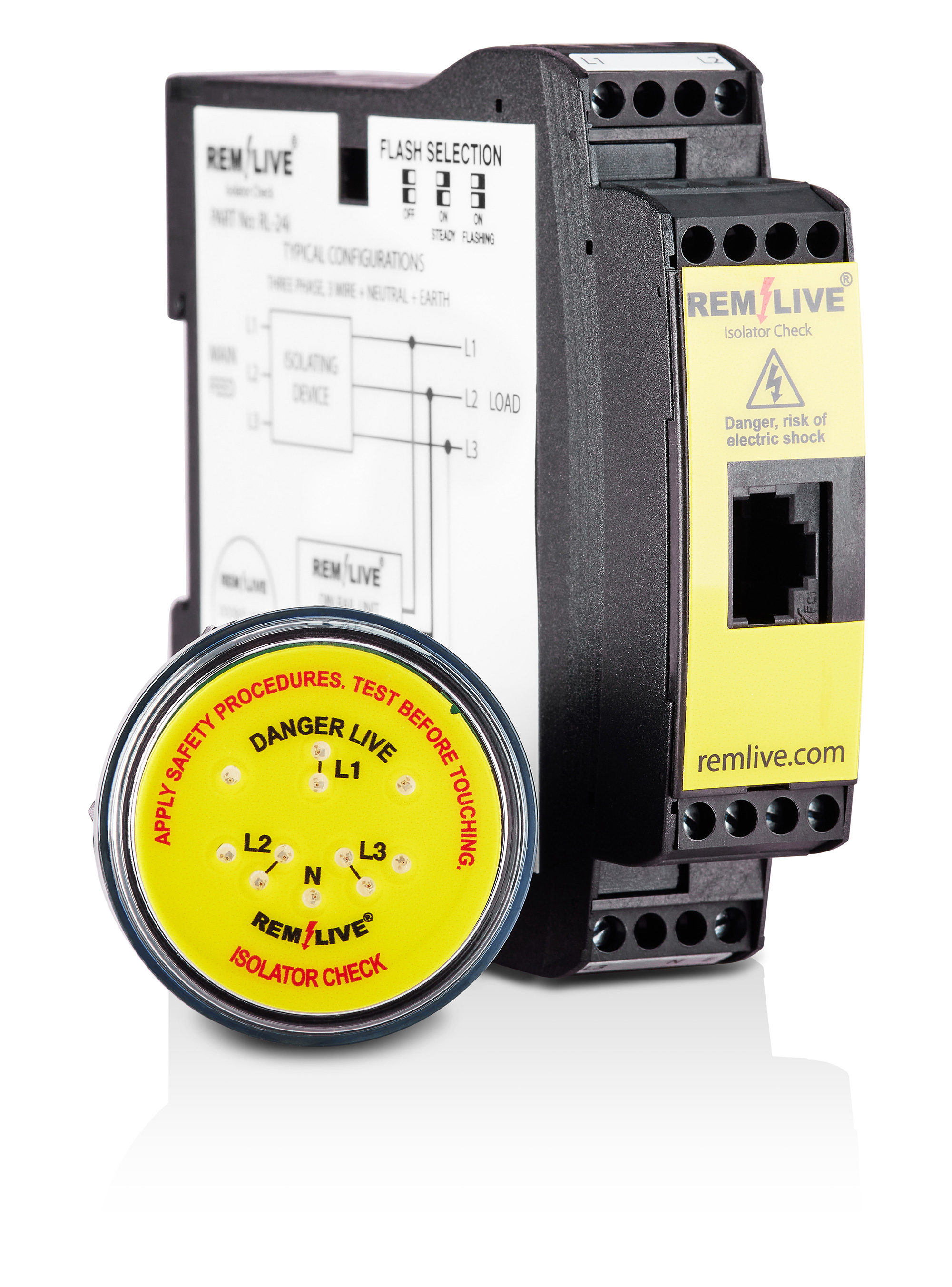
The door display unit is designed to fit through the front of a control panel so that the user can see the phase live/isolation status via LEDs. The display unit consists of bright flashing LEDs to attract the user’s attention, displaying the live/isolation status on the front of a control panel. The presence of all three phases (L1, L2, L3) and neutral are represented individually by LEDs on the door display unit, which assists with fault finding and enables users to see at a quick glance that all three phases are live. Low voltage (3.8V DC) to the door also ensures maximum safety for operators.
Features of the REMLIVE live line indicator include:
- Provides visual confirmation of correct isolation
- Broad range of voltages monitored: 24-1000V AC & 26-1000V DC
- 1000V AC Cat III and 690V AC Cat IV configurations
- 1000V DC Cat III and 600V DC Cat IV configurations
- Install in new or existing control panels with ease:
- 30.5mm door mount unit
- 22.5mm wide DIN-rail mount display unit
- Compliance with IEC 60204 – Safety of Machines
- Super bright flashing LEDs to grab users’ attention
- Consistent flash rate, every second
- Dual redundant internal surge protection
- Maintenance free
- Fully IP 66 certified, ensuring your switchboard maintains its overall ingress protection rating
- Housed in a robust V0 rated enclosure, selected for its durability and protective, insulation and zero halogen properties.
Contact information
NHP Electrical Engineering Products
Tel AU: 1300 NHP NHP (1300 647 647)
Tel NZ: 0800 NHP NHP (0800 647 647)
Web AU: www.nhp.com.au
Web NZ: www.nhpnz.co.nz
Email AU: nhpsales@nhp.com.au
Email NZ: sales@nhp-nz.com
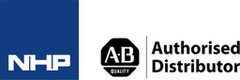
As a leading supplier of industrial and safety products, nothing is more important to us than helping you get the job done.