COMPANY INSIGHT
Sponsored by Torbjorn Idhammar, President IDCON INC
Reliability and maintenance management consulting and training company
How do we improve our overall production and maintenance reliability?
As reliability and maintenance management consultants, our team sees a lot of similar reliability projects being launched in different countries and industries.
In 95% of these reliability projects, the first question is:
“How do we start improving reliability?”
The second question is usually “How long is it going to take?” followed quickly by “How much is it going to cost?”
Some are hoping for a silver bullet that will solve all reliability problems, even overnight in some cases.
I have to tell them that it’s not that easy…that there is no magical checklist or a silver bullet that can improve reliability quickly and sustain it over time. There are many factors that determine how long an improvement will take.
Two of the most important factors to consider when beginning a reliability improvement journey are:
- Technical
- Cultural
Technical
Improving maintenance comes down to doing two things cost-effectively, they are:
- Reducing the amount of repairs
You do this by preventing failures through better essential care and condition monitoring practices such as lubrication, alignment, balancing, operating procedures, quality repairs, doing root cause elimination of failures, etc.
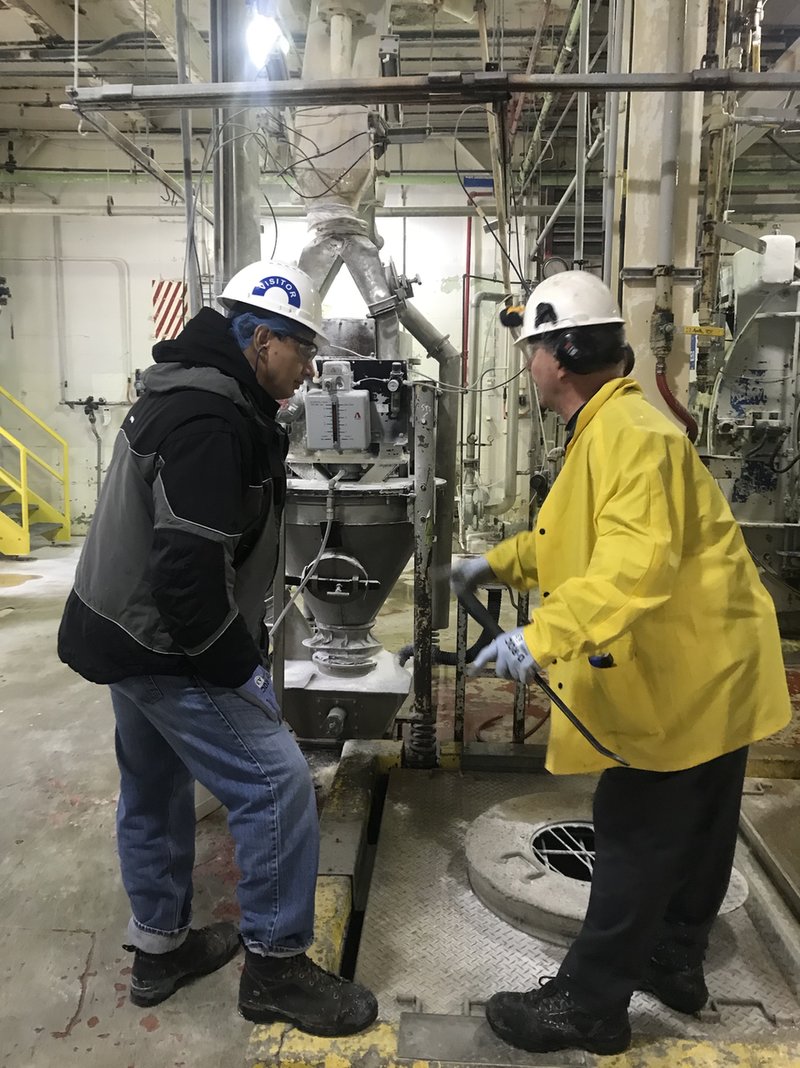
2. Execute repairs more effectively
This is done through disciplined execution of a work management process. In short, a plant needs to inspect – plan – schedule – and then execute work.
Work management must come early in improving reliability for the simple reason that all maintenance work, including lubrication, repairs, improvements, will go through the work management process.
If you don’t have basic work management processes in place- start now! It will prioritize and structure all maintenance work.
Image 2: Process workflow for Work Management planning and scheduling.
If you need help developing your workflows, give us a call and we can help you.
Cultural
The cultural factor is more important and often overlooked. Successful reliability and maintenance improvement projects have the following:
- A plant management team (Plant manager, Operations manager, and maintenance manager) DRIVING the improvement of work processes forward with a constant purpose.
- A plant team that accepts the direction of leadership and implements the direction on the floor.
Maintenance improvements is 90% about people and their behavior.
People don’t mind change, but they don’t like being changed. Therefore, it is critical to involve people early in the project, including the decision of where to start the reliability improvement project. For example, if you have buy-in to start condition monitoring, but hesitation around work management, perhaps you start with condition monitoring to get the momentum going.
Technically, I suggest you start with work management and condition monitoring if you don’t have this in place.
One final note, if you don’t know how well your organization is performing basic reliability and maintenance processes, it’s a good idea to have an assessment comparing your current practices with best practices. A good resource is IDCON’s 25 Reliability and Maintenance Questions to ask yourself.