COMPANY INSIGHT
Sponsored by Tegam
Data in 2021
Data is the answer and the problem. With valid real-time data, you can solve problems before they impact people or production. You can prevent errors and correct trends before they proceed out of bounds where they become dangerous. You can also protect yourself with hard evidence when regulatory agencies or attorneys are looking over your shoulder.
Food safety is a concern to all of us. Not only is it important to us personally but also collectively. The US CDC estimates that food born illness cost $15.6 Billion every year in the US and recommends using data to evaluate and revise foodborne disease prevention strategies and policies.
“What we got here is failure to communicate.” Captain, Cool Hand Luke
In food safety, no single parameter is more important than temperature. Food storage, preservation and preparation all involve critical control and seamless transition. It is not enough to store food properly in a freezer only to let it get warm in a staging area or transport vehicle. A full HACCP plan will identify the critical points, but now they must be documented to demonstrate control. Having a processing system that consistently produces safe and desirable food is not sufficient; you need to provide the hard evidence that you know it to be true over time.
The prevailing method for documenting process control is still pencil and paper. An operator will take a temperature with a sophisticated (or not) thermometer and then write the results down on a clipboard, sticky note or even their hand. When you look at the hardware cost of such a solution, its appeal is obvious. However, you must ignore the cost of the inherent inaccuracy and labor. The collected data can get reviewed by a supervisor or possibly entered in a quality management system for future reference. This further increases the labor costs involved. In many cases, the time lag from measurement to evaluation is a full work shift. If a noncompliance event occurs, it may require the full shift of production to be sequestered or lost. When all the labor costs and opportunities for error are considered, the cheapest solution is actually the most expensive with the worst performance. The goal of a control system is not to find problems after they occur but to prevent them from occurring in the first place. How then is your HACCP system made to operate in real time?
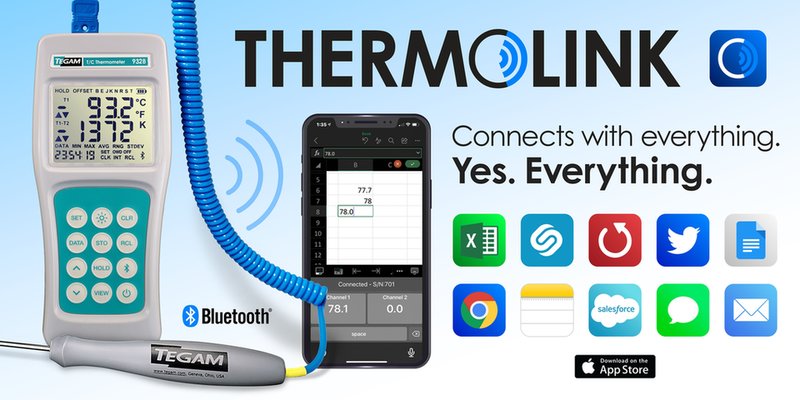
The recipe for real-time documenting HACCP systems involves custom software and expensive consultants. Workers are now required to carry a tablet and enter numbers directly into a system. The paper and pencil are replaced with just more expensive tools and unfamiliar methods. The significant challenges of requiring the operator to be the link between temperature measurement and system entry guarantees such a level of cost, inaccuracy and extra effort that it gets a negative reaction from both the production floor and office.
Systems that require extra duties of production workers are poorly received in an environment of higher productivity goals and safety compliance. The ideal solution would reduce the burden on production workers while providing accurate electronic documentation in real-time. In addition, it would also need to eliminate the reliance on internal or external software consultants and not restrict the choices in software platforms. Sure, and while you are at it, could you throw in some flying pigs.
Easier than looking for winged bacon or finding a pencil, there are current alternatives to closed proprietary systems with large price tags. Presently available thermometers allow them to be connected to any software that is currently being used on the production floor. If you are still reliant on paper and pencil, you can switch to paperless in a day by using any spreadsheet or document editor without IT support. Later, if you decide to move to one of the splendid Quality Management softwares, you can do so without retraining operators or buying new hardware.
The need for digital transformation has been known. Supply chain partners, regulatory agencies and business contingencies have long demanded access to data. The barrier has always been cost both of implementation and maintenance. Finally, there are emergent temperature measurement solutions that target all these concerns. They produce more accurate measurements and real-time electronic documentation while reducing the effort which needs to be expended by the production worker.
Contact Information
Tegam
Tel: +1 440 466 6100
To find out more, visit: www.tegam.com
Email: sales@tegam.com
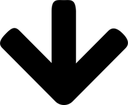
BACK TO TOP