Automation | Meat
Will automation be the saviour for US meat processing?
Production rates have declined due to the coronavirus outbreak, with meat processors in the US either closing plants or operating with a reduced workforce. Simon Creasey investigates how automation could be the solution for meat processing in the US, and looks to the impact it could have in the future.
At the height of the Covid-19 lockdowns, food supply chains across the world were placed under immense pressure. The strain was too much for some, which buckled amid unprecedented demand as consumers looked to stockpile goods.
One supply chain that particularly struggled to meet demand was that of the US meat industry – and not just due to stockpiling. In April and early May, US meat production slumped as workers were unable or unwilling to go to work.
US meat processors saw hundreds of employees test positive for the novel coronavirus. The sector has appeared to be a hotspot for Covid-19 infections, in part due to the lack of automation seen in the industry compared to other categories.
As infection rates rose, parts of the US meat industry faced criticism for its production processes. To try to protect staff, some manufacturers temporarily shut plants for deep cleaning and to implement more health-and-safety measures.
Adopting automation in response to the pandemic
“Pork and beef slaughter were the hardest hit, with plant closures and employee absences driving weekly slaughter declines of as much as 35% versus the year-ago period, whereas most poultry plants have seen only minor disruption,” says Christine McCracken, executive director for the animal-protein industry, at Rabobank, the Dutch financial services group.
The industry has now nearly recovered to full production, but according to McCracken, workforce issues linger. “Plants were able to implement distancing practices within the plant, which together with health screening and safety measures like masks were able to limit further employee risk. Even so, there are some at-risk employees that are unable to return to the plant and employee absenteeism remains a challenge.”
As a consequence, a growing number of US meat companies are exploring and/or ramping up the amount of automation they use in their plants. Tyson Foods, the US meat major and one of the world's largest, believes the industry will likely quicken its efforts to increase the use of automation in production facilities.
“I do think that, over the course of time, the amount of automation will in fact continue to increase, particularly in some of the more difficult jobs and positions,” Noel White, Tyson’s CEO, told investors in early May.
We envision a future where automation will impact the majority of tasks.
White pointed to Tyson’s investment in “vision technologies” to minimise any foreign objects in the production process. He added: “We’re working in the de-bone area within poultry, we have a number of initiatives within beef and pork. I believe it's not only us as a company. I think the industry will continue to look for solutions through automation. I think it will likely accelerate from this point."
US agri-food giant Cargill, one of the largest beef suppliers in the country, argues “the future of protein will absolutely include automation”.
“We’ve already seen these advances in grading, packing and plant logistics tech at work,” a Cargill spokesperson says. “The reality is, producing animal protein means managing live animals that vary in size, weight and other dimensions that make automating the initial part of the supply chain complex. As we get closer to finished products, the opportunities for automation increase.”
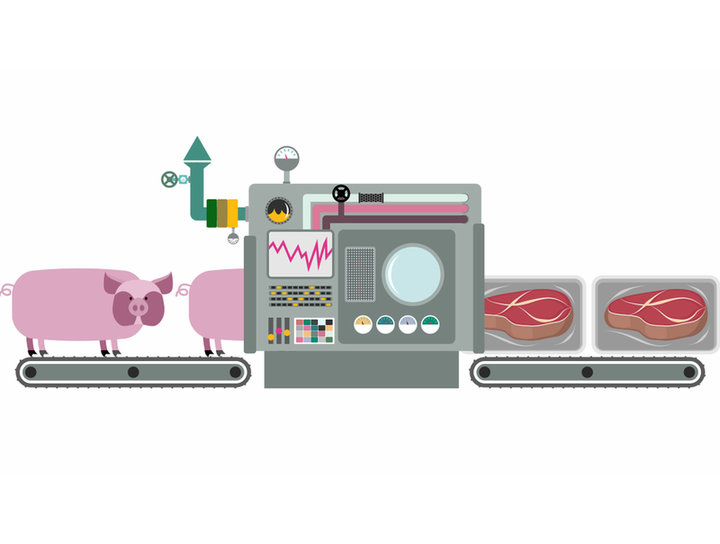
The Cargill spokesperson says company representatives are “meeting with innovators nearly every month making sure we have the latest insight that helps focus on people and food safety, address labour shortages and ensure we deliver for customers and consumers”.
It’s a similar situation at Smithfield Foods, the US pork processor owned by China’s WH Group. A spokesperson for Smithfield says by 2050 the company expects advanced robotics, connectivity on the factory floor, data analytics and AI will be at the forefront of modern meat manufacturing.
“We envision a future where automation will impact the majority of tasks, but that some manual facets of facility operations will persist,” says the spokesperson. “We invest tens of millions of dollars or more each year in capital improvements to facilities and equipment, focusing on the safety of our products and protection of our employees while simultaneously enhancing production.”
Smithfield says it has already invested significant amounts in new robotics technology and other equipment that enables higher levels of automation to occur.
“For example, we’ve added into our processing facilities an automatic handling system that allows our employees to cut meat from the bone safer and more efficiently,” a spokesperson explains. “Automatic rib pulling and cutting systems also provide value via vision and x-ray technologies that select the optimum rib cut from the pork belly, improving yield.”
The early bird gets the worm: poultry is one step ahead
While processors of red meat have started to make inroads in terms of automating their processes, experts say the poultry industry has been quicker to adopt and embrace automation.
Mike Cockrell, treasurer, chief financial officer and chief legal officer at US poultry producer Sanderson Farms, says the company spent $70m in its 2019 fiscal year automating what he describes as “the front end” of the factory.
“The live chicken arrives at the plant, it is re-oriented into a shackle and no-one touches that chicken again until it comes out of the chiller,” Cockrell explains. “That chicken is slaughtered, de-feathered, the feet are taken off it, it goes into the eviscerating department where machines eviscerate that chicken and harvest the livers, the gizzards and the hearts and then that empty carcass goes through a chilling process.
“When that chicken comes out of the chiller, an hour-and-a-half or so after it enters, it is wholesome and you can sell that whole chicken and no-one has touched it since the hanging dock.”
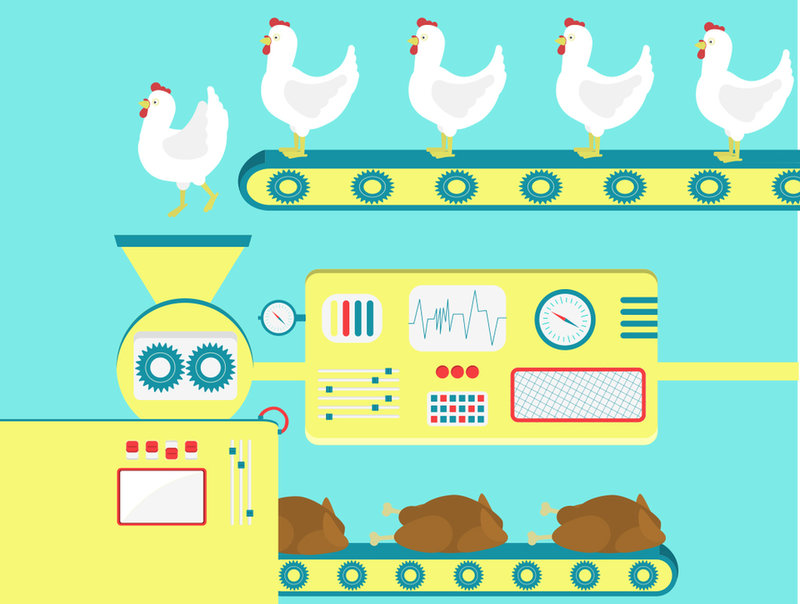
Cockrell believes part of the reason the US poultry industry escaped some of the “doomsday scenarios” experienced by red meat processors was because it’s not as reliant on physical labour to turn a live animal into a sellable product. However, he explains not all parts of the poultry production chain can currently be automated.
“With most of our chickens, the breast meat is de-boned and we produce boneless, skinless breast meat – and all of that is done by hand,” says Cockrell. “There is equipment out there that will automate that process, but it is still inefficient and it is not fully developed.
“The breast meat is the most valuable part of the chicken. It’s the highest price, it’s the highest margin and the better yield we can get off of that the better, but at the moment the yield disadvantage of the equipment is still such that it pays just to hire the people to do it.”
He says at some point a “brilliant young robotics engineer” is going to come along and invent a robot that can undertake that process more efficiently and, when they do, it will be transformative for the poultry industry.
Red meat processors will be similarly watching and waiting for technology to come along that allows greater levels of automation to occur in their daily operations. Until that time, Cockrell fears that these processors could struggle to handle the ongoing fallout from the pandemic.
“Until there's a vaccine for the Covid-19 virus, I would suspect you're going to continue to see distancing in all of these plants. I imagine that some of the measures we put in place like face masks and face shields are going to become best manufacturing practices that we will follow forever and unless the red meat industry can discover a way to put more automation in they're going to continue to have issues.”
Capital investment and availability still a barrier for smaller processors
For the larger meat processing groups such as Sanderson, Cargill and Smithfield it is easier to justify the capital outlay required to increase automation on the factory floor as and when suitable equipment becomes available, but it may be beyond the financial reach of some of the smaller US processors.
However, when the numbers do stack up, it’s anticipated more and more meat processors will explore the advantages of ramping up automation.
“While our members are still working to get back to normal and to ensure the men and women who work in their facilities are safe, if the cost-benefit analysis makes sense, packers and processors could turn to more automation,” says a spokesperson for national trade association The North American Meat Institute.
“The machinery will have to be sophisticated to process animals because no two are alike, but meat and poultry companies are always willing to innovate when protecting workers or improving food safety.”
As labour costs continue to increase and with lost productivity a growing issue, the new equipment is more easily justified.
It’s a view shared by Rabobank’s McCracken. She believes all US meat processors will continue to explore the greater use of automation in plants where possible, but there are a number of different hurdles that need to be overcome before automation becomes more commonplace in the industry.
“Part of the issue is availability, as the lead time on equipment can be several months and, with so many inquiries, many companies are unable to deliver for a plant’s immediate needs,” she says.
Another key challenge is the practicalities of adoption within a plant “with so many older lines where the equipment is needed, housed in very tight spaces, installing a new piece of machinery is not practical,” McCracken adds. “There is also the issue of cost, although as labour costs continue to increase and with lost productivity a growing issue, the new equipment is more easily justified.”
These challenges are not insurmountable and if the US meat industry wants to avoid a repeat of the problems it was faced with at the height of Covid-19’s spread, the adoption of automation appears to present a sensible way forward.