COMPANY INSIGHT
Sponsored by Torbjörn Idhammar, President IDCON INC.
Preventive Maintenance Best Practices
“How can downtime be avoided?” is a question we often hear when we tour plants. There is no silver bullet for ending production stops or improve Preventive Maintenance (PM). It takes combined efforts together with an organized approach to see results.
For the purpose of understanding this article, IDCON’s definition of Preventive Maintenance is all actions that can prevent failures or predict failures early. Our definition of PM includes preventive actions as lubrication, alignment, cleaning, and operating practices as well as condition monitoring (inspections).
Why do many plants struggle with their Preventive Maintenance strategy? In many cases we’ve found the root of the struggle points to a lack of discipline in execution. But also, PMs haven’t been well defined (documented) using a structured approach. It is not uncommon to see too many PMs where some equipment has multiple overlapping PMs while others completely lack PMs. It is also very common to see inspections scheduled on a shutdown when they should be done on the run. For example, why would you do a centrifugal pump inspection on a shutdown when you can see exactly what the pump is doing on-the-run with vibration, temperature, noise, and pressure checks? If you don’t have pressure gauges installed, install them, I’m pretty sure they are cheaper than the additional downtime and labor for shutdown inspections.
IDCON has defined the essential elements of Preventive Maintenance (PM) in our Current Best Practices (CBP) assessment tool. There are roughly 80 best practices in the PM section of the assessment. For this article I have combined some best practices into 4 key items to convey the core essence of PM. If you think your PM program is in disarray, I suggest you do a quick self-assessment as you read this and start with these key items.
- Have the PM’s been evaluated using a structured approach that takes the consequence of break-down, shutdown vs off-line, failure development and inspection frequency, and the technical content of the PM in consideration?
- Is the alignment of shafts well executed in the plant (important in process industry)?
- Are lubrication tasks executed well in the plant?
- Are mechanical & electrical, equipment well inspected. Are instruments are calibrated and are loop checks done well?
When we score the PM process in our assessment, we score the work process. A work process is something that is:
- Documented
- Executed
- Followed-up upon. (with a Key Performance Indicator (KPI), or some other way)
We put most importance (70%) on the Execution when we score.
If 100 is perfect, 75 very good, 50 is reasonable, 25 is in great need of improvement and 0 non-existent. How do you score?
On average, the plants scored 37.5 out of 100 in PM best practices. It’s no wonder these plants were reactive and experienced equipment failures.
1. Have the PM’s been evaluated and well-documented?
PM’s are often documented and put into a CMMS system right after a break down. There are often a lot of pressures on the frontline of the organization from the leadership after the break down. The person writing the PM is often stressed and not completely sure what to do.
Part of the problem is that there is seldom a guide for how to generate a PM, it is often 100% based on experience. It’s common that the following are often missed.
- We forget to check if there already are PMs in the different systems we have (vibration, operations, CMMS, lubrication system, etc.). Since we don’t check, we end up with many duplications.
- For inspections: There is little consideration to the failure developing period in order to set the inspection frequency. We tend to set up PMs on a very high frequency in order to safeguard us against re-occurring events. However, if the Failure Developing Period is very long, we end up doing unnecessary work.
- For fixed time overhauls: There are seldom solid information about the life of the component we decide to change out. It is typically based on how long the previous component lasted. The problem with this approach is that most components have a random life (For example: Bearings have a life expectancy of 1-25 years, so when do you change them?)
- The content is poor since we don’t take the time to research how to do the PM or inspection. It is common to see PMs such as “PM Motor”.
- PMs are traditionally done while equipment is shut down. The mindset is not to move inspections to on-the-run. In our experience, 60-70% of inspections can be done on-the-run for heavy process industry and municipals. It is different for the manufacturing industry such as assembly lines, plants with a lot of CNC machines, and/or electronics manufacturing.
2. Shaft alignment
In a world-class reliability and maintenance organization, all alignments are done to 0.002 in. (0.05 mm) for equipment running below 3600 rpm and 0.001 in. (0.025 mm) for equipment running above 3600 rpm. There is typically a well-defined alignment standard explaining how to set up, clean, check for pipe strain, check for soft foot, etc.
Take a tour of your plant. If alignment is done well there are jacking bolts (push bolts) installed on all motors, gears, and other equipment of significance. Bases and foundations are in good condition and no more than four shims are used under the motor feet. Overall vibration level is low in the plant (0.1 in./sec unfiltered average in the horizontal plane). As a tracking indicator, see if alignment records are kept for each alignment job.
Shaft alignment is obviously more important in a plant with a lot of rotating equipment.
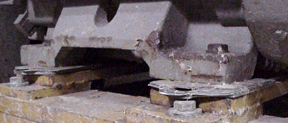
Image 1: Tour your plant and look for signs of good/ bad alignment. Above is a motor with too many shims (causing soft foot), the motor has been “hammered” into alignment since push bolts are missing. The base looks like it probably is not completely flat.
3. Lubrication
Lubrication is a key factor for most industries to achieve high reliability. The correct tasks for greasing, oil changes, and oil sampling should be documented and executed correctly.
The end-game for good lubrication is to have the correct, clean lubricant in the equipment. In order to get the correct and clean lubricant in the equipment, it is critical to:
- Evaluate the volume and type of lubricant that is appropriate for each lubrication point. This is typically done through a lubrication survey.
- Lubricant must have the right cleanliness when purchased or, alternatively be filtered when delivered to the plant.
- The lubricant must be stored correctly in order to keep its cleanliness level
- The lubricants must be handled correctly in order to avoid dirt to enter the lubricant containers.
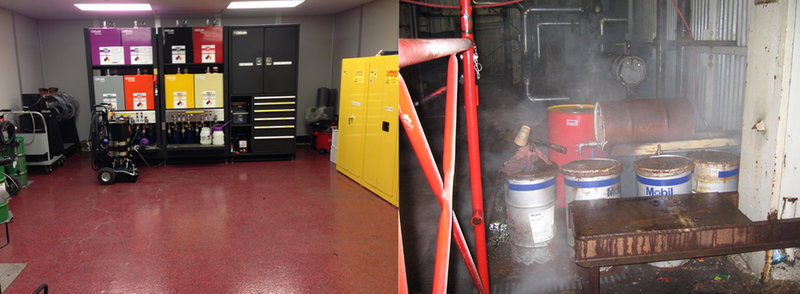
Image 2 & 3: Storage of lubricant is critical for lubrication cleanliness and properties. To the left we find a clean, air- conditioned lubrication storage with the correct containers, unlike the right where we find a lubrication storage that needs improvement.
4. Are inspections (condition monitoring) done well?
In a top-notch plant, inspections are documented and completed according to schedule. The plant is using an inspection list or, even better, a handheld device. The list or handheld describes exactly what to do for each inspection. The inspections are a combination of measurement of the condition (for example with vibration, temperature, flows, Current etc.) and subjective (look, listen, feel, smell) inspections.
Check if your plant is performing according to world-class reliability and maintenance standards, for example, check the following:
- Do we have condition monitoring routes covering all necessary inspections?
- Are the inspections being performed (By Electricians, Mechanics, Instrumentation, Operators?)
- Are we calibrating instruments and performing control loop checks (or have smart valves?)
- Do we use simple inspection tools such as a stroboscope, infrared thermometer, vibration pen, industrial stethoscope, bright flashlights (500,000 candela), and inspection mirrors?
- Can we inspect couplings, belts, and chains on the run, or do guards make it impossible?
- Do we use motor testing, vibration analysis, infrared thermography, and ultrasound effectively?
- Are people trained in basic inspection techniques?
- Do we have a system to follow compliance and quality of execution of tasks?
If you think your plant can be helped with some outside expertise to look over your preventive maintenance system. Please, give us a call 919 847 8764.
Learn how other plants have implemented Preventive Maintenance Strategies at the IDCON Reliability and Maintenance Conference September 23-25, 2019 in Raleigh, North Carolina