Company Insight
Sponsored by NHP Electrical Engineering Products
NHP - Specialists in electrical and automation products, systems and solutions
With more than 55 years of electrical and engineering industry excellence and over 20 branches across Australia and New Zealand, it is NHP’s local people and footprint that helps us to understand your specific project needs, no matter how big or small.
Not only is NHP the long-standing exclusive Authorised Distributor for Rockwell Automation throughout the South Pacific region, we are now also the sole Authorised Service Provider in this region for the automation giant. Through our SMART digital devices, NHP can assist you to achieve better visibility into processes, data and analytics. We have helped thousands of customers on their digital transformation journey, enabling the Connected Enterprise.
When it comes to finding a local partner with a global network for your next project, choosing NHP will unlock a world of expertise across electrical and automation products, systems and solutions.
NHP Services and Solutions – offering so much more than quality electrical and automation products
In conjunction with our major supply line partners, NHP offers our customers services and training solutions, leveraging industry and technology-specific expertise, to maximise operational investments, improve your business and meet your everyday needs.
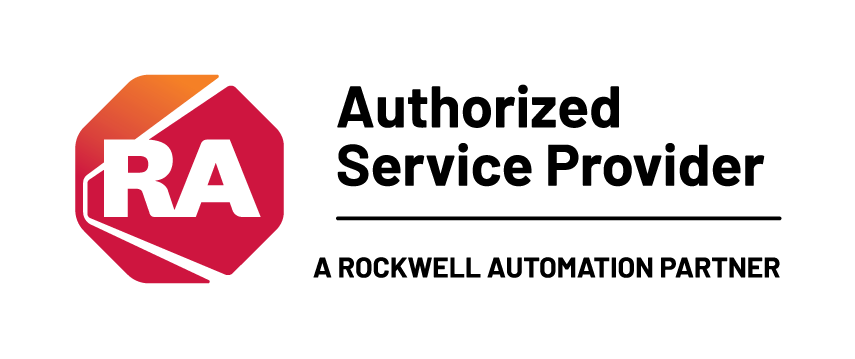
Installed Based Evaluations (IBEs)
An Installed Base Evaluation™ provides better knowledge for you to make informed decisions, thanks to insights into your installed base. This is much more than simply counting parts. It’s a thorough analysis of your critical plant assets and their condition.
This service provides the knowledge needed to help you make data-driven decisions regarding the support and obsolescence management of your installed base assets. With an IBE, we can help you better understand and pinpoint your lifecycle risk by site, area, line, machine and panel. By optimising your maintenance, repair and operations, we’ll help ensure you have the right parts, in the right place, at the right time.
An IBE will enable:
- Thorough analysis - the IBE goes beyond simple part counting and provides a comprehensive analysis of critical plant assets and their condition;
- Data-driven decisions - the service equips customers with the knowledge needed to make data-driven decisions regarding the support and obsolescence management of installed base assets;
- Lifecycle risk identification – you’ll be able to pinpoint lifecycle risks by site, area, line, machine and panel, helping you to proactively manage and optimise your assets;
- Optimise maintenance and spares - by optimising maintenance, repair and operations, the IBE ensures you have the right parts in the right place, at the right time, reducing costs and increasing uptime;
- Inclusion of non-Rockwell Automation products - the IBE collects both Rockwell Automation and non-Rockwell Automation products, creating a comprehensive plant hierarchy model for the facility;
- Consultative approach - the IBE delivers analysis and recommendations through a consultative approach, helping you to understand the impact of equipment updates and spare parts management strategies;
- My Equipment dashboard - access to an online tool that provides easy to read dashboards with the ability to maintain the asset list as changes occur on site, giving an updated analysis to lifecycle risk and spare parts management.
To start your IBE journey, email us at nhpservice@nhp.com.au
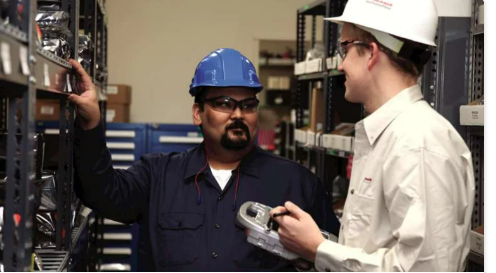
Cybersecurity services
The security landscape is ever-changing, so you need a partner whom you can trust and is transparent in approach to help you manage the constantly evolving risk. NHP’s industrial security portfolio and services will help you assess, implement and maintain ICS security within operations and enable transformational technologies that rely on enterprise connectivity – read more detail in the section below.
Technical training
With over 500 technical training courses, seminars and workshops held annually across Australia New Zealand, NHP can help to improve your knowledge in the areas of automation and process control, hazardous areas, safety standards, drives, vibration, PLC software, enclosures, computerised maintenance management systems and much more.
On-site support
NHP, backed by Rockwell Automation, offers a range of on-site field service solutions to suit a wide range of needs. Whether your need is for installation and commissioning, migration, emergency breakdown or lifecycle services, NHP has engineers and technicians placed in strategic locations throughout Australia and New Zealand to respond to your needs.
Repair and remanufacture
Are you confident that your spare parts will operate correctly when needed? NHP takes pride in our repair and remanufacture capabilities. Our repair technicians or supply partners will repair or remanufacture your equipment, using replacement parts that meet or exceed the original design specifications.
Simple, flexible and worry-free service agreements
NHP offers a range of tailor-made service agreements, from spare parts management, on-site and phone support, repairs and preventative maintenance.
Savour the taste of cybersecurity in the food and beverage industry
Security breaches in the food and beverage industry can impact production in unique ways. Attacks can occur on key operational systems such as refrigeration, materials might be misdirected, or recipes may be tampered with or stolen. This can have consequences beyond product and financial losses - a specific cybersecurity strategy is crucial to minimise the risk of product quality and safety issues.
In May 2021, a ransomware attack on a major US meat processing plant knocked out their ability to supply roughly 20% of the United States’ meat supply. Threat actors encrypted the company’s systems and data, then demanded a ransom of $11 billion USD to restore access. This followed an estimated 40 attacks on food producers in the previous 12 months.
It was such a familiar story that the FBI began alerting US food producers, processors and manufacturers via an industry-specific notice that criminals are carrying out focused ransomware attacks targeting this sector.
The food and beverage sector requires proactive cybersecurity protection according to the challenges that they are facing.
Challenge 1: avoiding downtime and damage from cyberattacks
Successful cyberattacks on operational technology often result in downtime, which is extremely costly for food and beverage manufacturers who produce hundreds or thousands of products per second. Threat actors who gain control of plant floor machinery could also adjust product recipes and ingredient ratios that would impact product quality and safety.
Challenge 2: modernising manufacturing operations
In an era dominated by digital innovation, the food and beverage industry has witnessed a remarkable transformation. From online ordering and delivery to automated processing, technology has revolutionised the way this sector operates. However, with these advancements come new challenges, one of the most critical being cybersecurity. As the industry becomes increasingly interconnected and reliant on digital systems, the need for robust cybersecurity measures is more evident than ever.
Challenge 3: removing legacy plant floor computer risks
Food and beverage manufacturers often have legacy production systems which make deploying the latest cybersecurity protections difficult. The good news is that secure information convergence with an aging infrastructure is possible. An industrial data centre (IDC) arms food and beverage manufacturers with a way to manage these legacy plant floor computer risks. Even outdated operational support systems, multiple distributed computers with their own operating systems and other legacy infrastructure can be converged into an IDC. This allows strong cybersecurity support technologies and processes, such as 24/7 threat detection and frequent asset inventory audits – daily, hourly or even real time – to be deployed to help secure operations from cyber incidents and to preserve product quality and safety.
Challenge 4: proactively detecting and responding to attacks
Responding quickly is challenging because threat actors employ tactics to evade detection. Perpetrators know better than to make their presence on a network evident until they are able to carry out their malicious intentions. Evasive techniques include using commercially available tools to move laterally through networks and establish persistence.
Threat detection solutions can detect malicious activities at any stage of an attack, helping to stop hackers from their nefarious work, such as conducting reconnaissance to executing malicious payloads. Plant floor anomalies, such as communication changes between industrial assets, can also indicate a lurking actor who may be preparing to attack. When time is of the essence and vast production losses are on the line, food and beverage manufacturers need this real-time threat detection capability.
Meeting the challenges
Rockwell Automation has built a global practice around industrial cybersecurity, securing some of the largest food and beverage industrial organisations in the world. As the exclusive Authorised Service Provider for Rockwell Automation in the South Pacific, and in alliance with Claroty and Crowdstrike, NHP can help your business to identify cybersecurity risks to your industrial assets through risk and vulnerability assessments including penetration testing, then develop and run the right program for your specific infrastructure and company needs.
A game changer in electrical safety!
The most likely time for an arc fault to occur in a switchroom is during electrical and mechanical operations, such as switching, isolation and racking of circuit breakers. It is common practice in the industry to use personal protective equipment for operator protection during these operations, however it is more effective to isolate the operator entirely from the arc fault hazard. Isolation involves personnel being separated from the energised electrical equipment and conductors.
NHP's TemRack iR is a fully integrated automated motorised racking device, which enables remote racking of the Terasaki TemPower 2 AR ACB body in and out of its associated carriage. The automated racking function permits safe isolation of the ACB with zero physical interaction between personnel and the ACB, thereby reducing the risk of exposure to explosive arc fault events and high incident energy.
Minimise risk and maximise safety with NHP's TemRack iR.
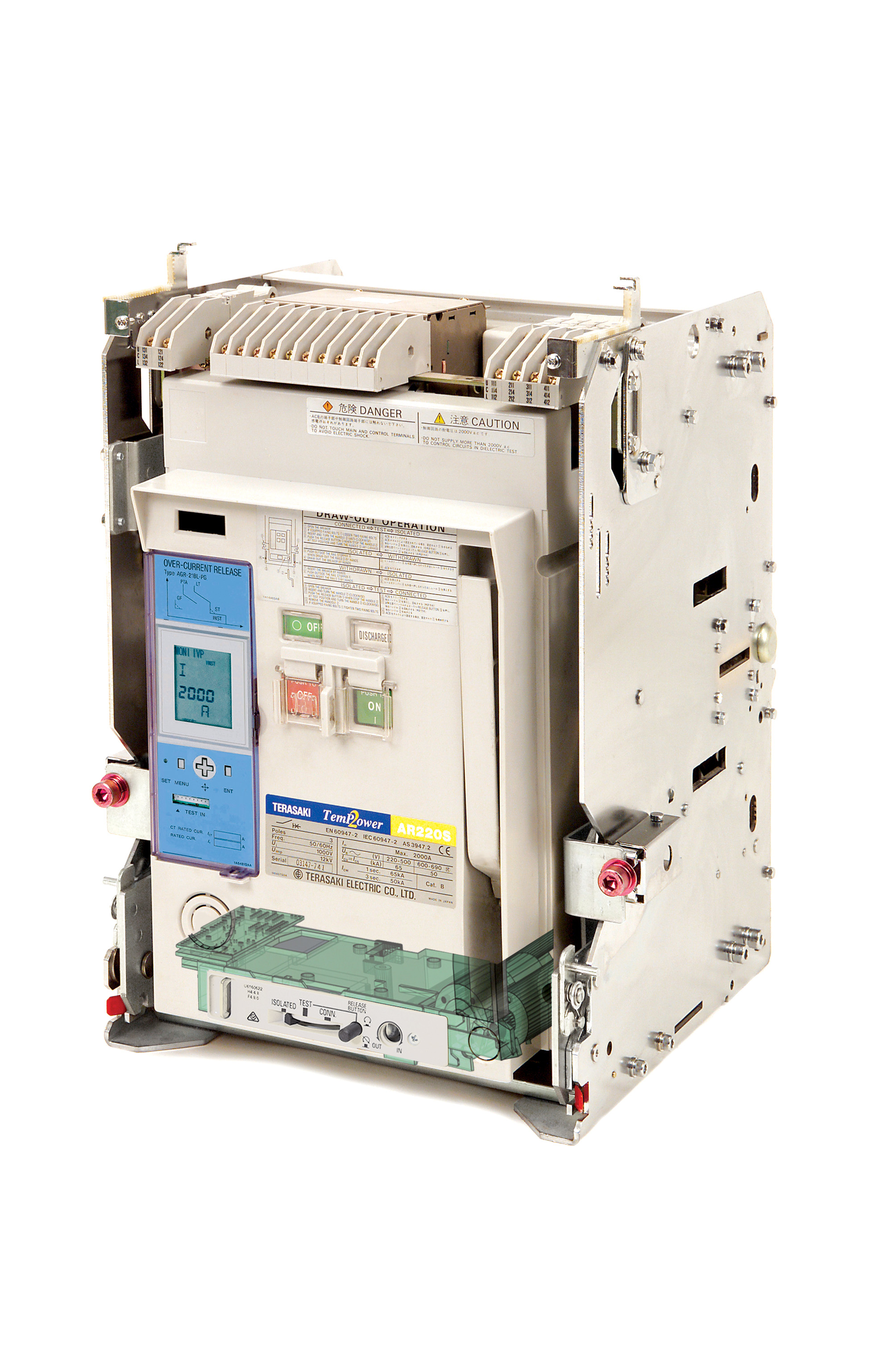
Medium voltage solutions that are built to last!
NHP’s MV products and solutions include a range of switchgear manufactured in Belgium by our quality manufacturing partner Switchgear Company (or ‘SGC’), transformers manufactured in Italy by Trafo Elettro and customised kiosk solutions manufactured in Australia by NHP. The MV switchgear is high quality and packed with safety features and the range consists of the ‘DF-2’ and ‘DF-2+’ air insulated panels and the ‘DR-6’ and ‘DR-6+’ gas insulated RMUs.
NHP’s MV transformers include both cast resin and oil immersed types, which can be supplied enclosed or unenclosed. NHP can also customise kiosk solutions, including full MV/LV kiosks, outdoor enclosed MV switchgear sub stations and outdoor rated enclosed transformers. Coupled with a local, experienced, customer centric team of MV experts, NHP excels at providing project solutions that focus on:
- safety for people
- reliability of product
- availability of power
- compliance to standards
- customisation of solutions to meet customer needs.
Features and benefits of NHP’s medium voltage range include:
- ‘Arc-Killer’ quenching system, which quenches an arcing fault in less than 50ms
- Visible earth switch and in line isolation
- Highest levels of safety when testing cables
- Cast resin transformers with arc mitigation by design reduce the risk of fire
- No need to externally vent arc fault gasses
- Switchgear with a 50 year design life
- Modern vacuum switching and load break technology
- Proven performance
- Sets a new standard for reduced partial discharge
- Most advanced method in HV winding fabrication
- Environmental and climate class tested
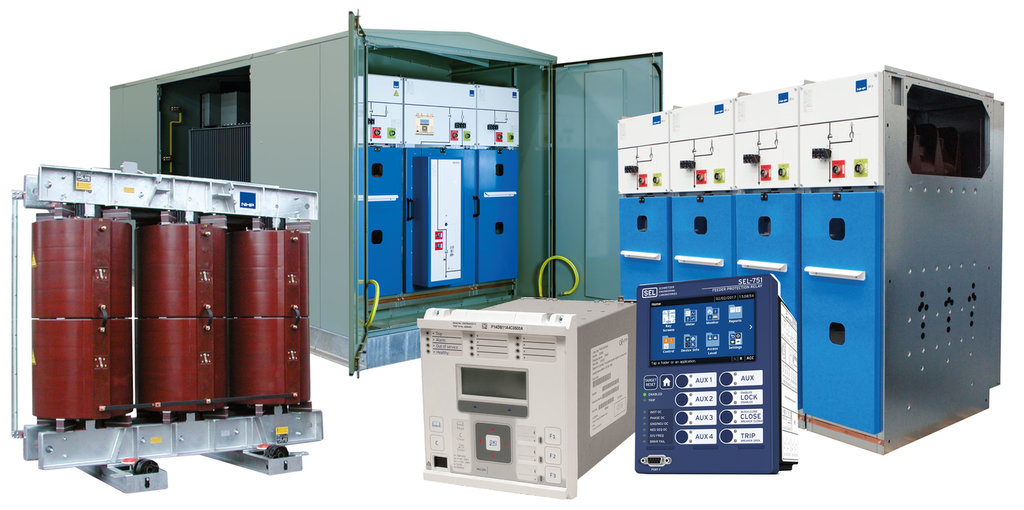
Contact information
NHP Electrical Engineering Products
Tel AU: 1300 NHP NHP (1300 647 647)
Tel NZ: 0800 NHP NHP (0800 647 647)
Web AU: www.nhp.com.au
Web NZ: www.nhpnz.co.nz
Email AU: nhpsales@nhp.com.au
Email NZ: sales@nhp-nz.com