Feature
Food majors harness AI in quest for efficiency
The world’s largest food makers are using AI to improve manufacturing, tackle waste and help forecasting. Simon Creasey reports.
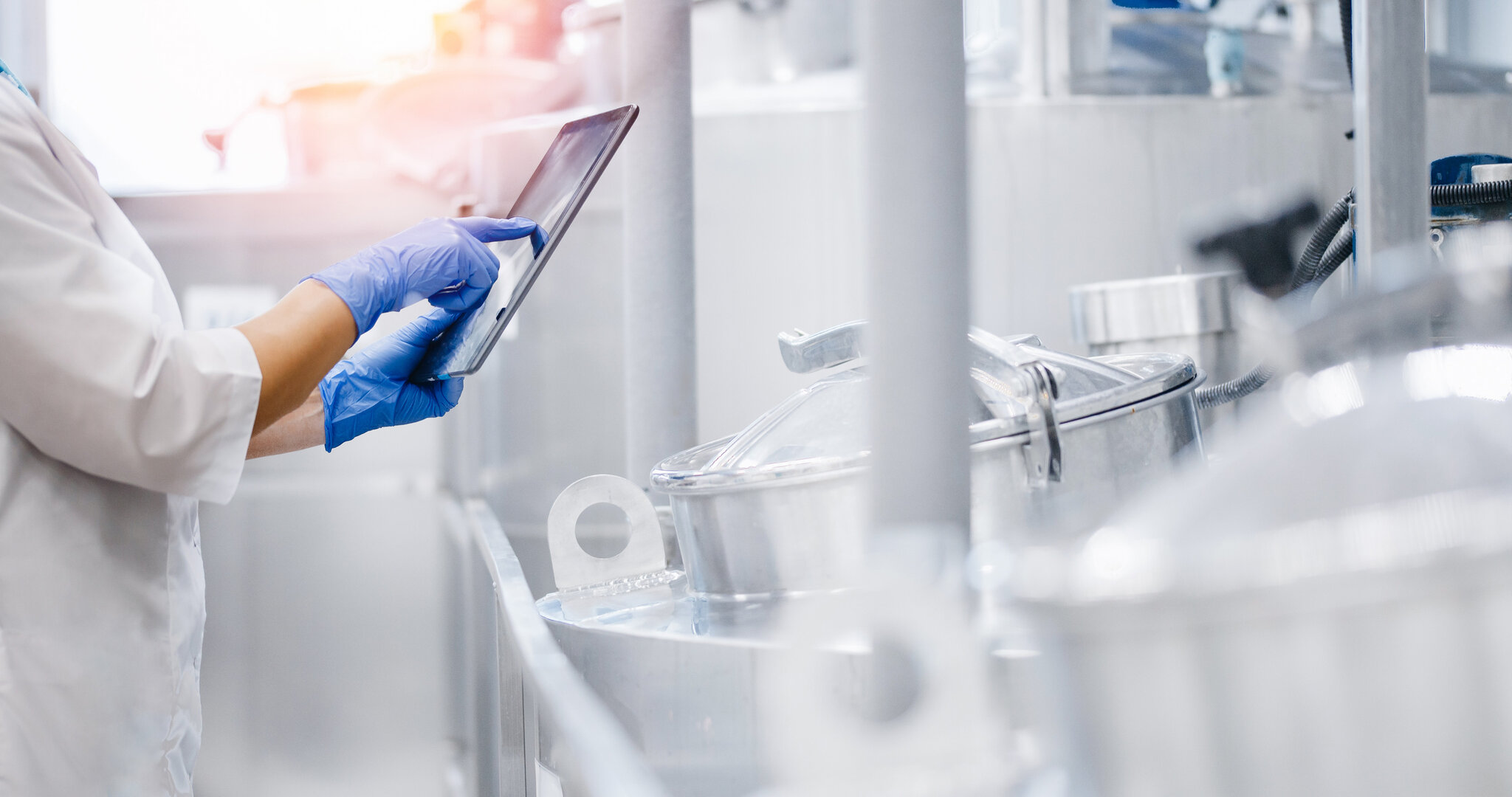
Over the past 12 months, there has been a lot of talk about the benefits businesses could potentially derive from the use of artificial intelligence.
Experts have speculated how the technology could be deployed and what improvements it could bring across different business processes and functions.
It is anticipated AI could deliver significant gains in areas like manufacturing and the supply chain and, in some industry sectors, the technology has already been deployed in these areas with varying degrees of success.
Projects underway
A number of the large food groups have already run trials or pilot projects employing AI in areas where it is perceived easy gains can be made. These areas are typically where businesses have historically gathered lots of data.
“One of the benefits with AI is it very quickly can analyse large amounts of data and identify trends and irregularities,” explains Mikael Bengtsson, solution strategy director covering the food and drinks sectors at cloud company Infor. “The same could in theory be made by humans but it would take much longer and likely be obsolete by the time it is ready.”
Bengtsson cites the example of an Infor customer that uses AI to improve their cheese manufacturing. “By collecting many different processing data points and then analysing them in close to real time, they can set manufacturing parameters to optimise the yield of the raw materials. In other words, they can produce more with the same, increasing profitability,” he says.
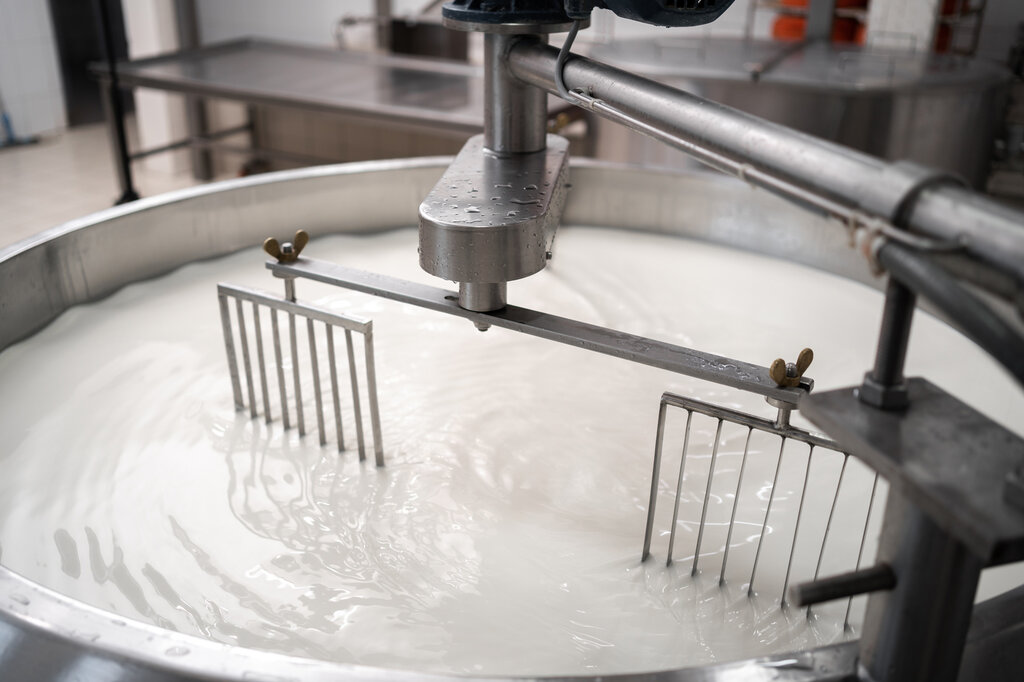
Another area where AI has been deployed by some food and drink businesses is machine maintenance. In addition to potentially playing an invaluable role in predictive maintenance, the technology can also be used to quickly make repairs to machines on the factory floor.
“When a machine goes down, the AI can begin to suggest to the mechanic or the operator what they can do in order to help fix the problem,” says Eric Whitley, director of industrial transformation at L2L. “So, it’s improving the processes and it’s reducing the amount of time it takes people to think about what the problem might be and how to solve the problem and, in some instances, it’s actually giving them the answer before they even ask.”
It’s improving processes and reducing the amount of time it takes to think about what the problem might be.
Eric Whitley, L2L
Abhinav Agrawal, global co-leader of AI monetisation at consultants AlixPartners, believes repairs, maintenance and training could be the areas where AI will make the biggest impact in the future.
“Every plant has standard operating procedures. They have all of the equipment manuals, training videos and lots of data but, when someone wants to find a specific piece of information, it’s very, very hard. This is where AI could be the game changer in some ways.”
Agrawal says AlixPartners has developed a module within its “smart factory” work on manufacturing through which it has run pilot projects and claims it’s achieved some “amazing” results already.
“So, if the machine goes down, it will show the person a 15-second clip from an eight-hour video that shows them what to do on a step-by-step basis,” he explains. “Now, it is not 100% accurate at the moment – what we are seeing is close to around 80% accuracy – but 80% is better than what we have right now and over time it will improve.”
Food giants plan further investment
Given the efficiency gains experts like Agrawal believe businesses can derive from rolling out AI, it’s not surprising to discover food companies that have already implemented the technology and have plans to embrace AI to an even greater extent in the future.
For Kraft Heinz, AI is part of its wider plans to “lead the future of food”. A spokesperson for the business explains: “Our ambition when it comes to AI and automation in our supply chain operations is to continue exploring, testing, and implementing these types of tools and technology to help us gather real-time insights and information across our supply chain – to have this data immediately usable – so we can continue making strategic decisions and delivering value with speed and agility for our consumers and customers.
“As part of this journey, we built an in-house ecosystem to accelerate and improve our supply chain. Using AI-powered real-time information and automation, this ecosystem enables us to get products into the hands of our customers and consumers faster than ever.
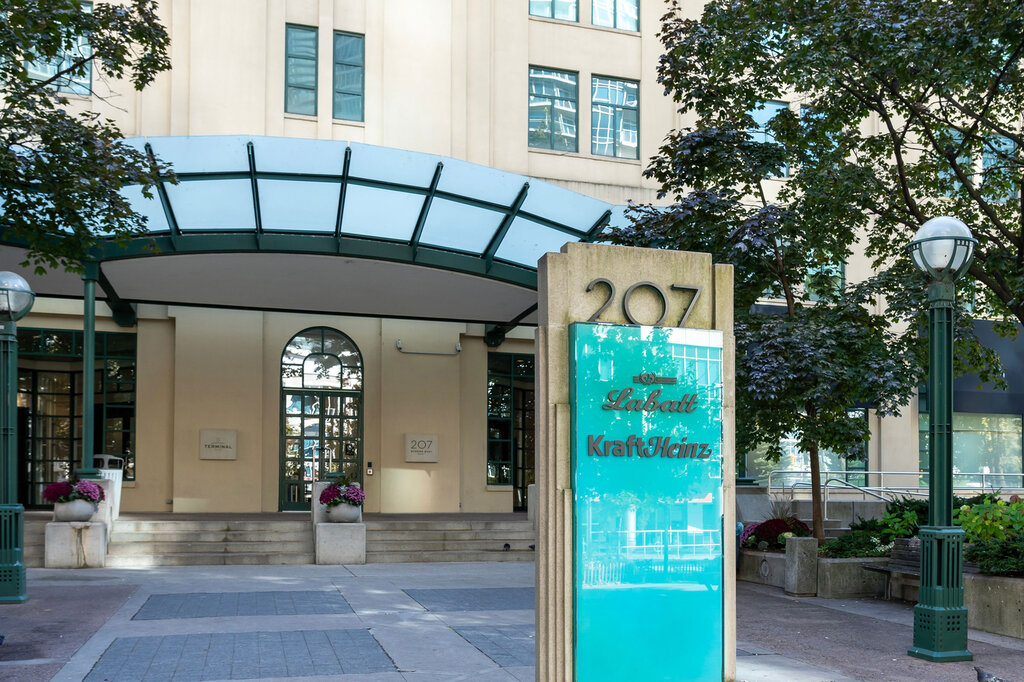
Credit: JHVEPhoto / Shutterstock.com
Within this ‘digital ecosystem’ is Kraft Heinz Lighthouse – the company’s ‘control tower’, which looks across the supply chain and uses AI to predict variables that could impact a product’s delivery path.
“The technology has significantly improved demand and production forecast accuracy, including improving end-to-end supply chain performance by boosting our sales forecast accuracy and inventory forecast accuracy and by reducing reaction time,” says the spokesperson.
Another food business that’s enjoying significant benefits from implementing AI is Kellanova, the snacks and international cereal arm of the former Kellogg Company. In 2022, the business decided to run a pilot AI project for process control at its facility in Wrexham in north Wales. It used the technology on its Krave cereal brand because it has a relatively simple production process and the end-to-end manufacturing of the product is relatively short.
“Incorporating data from our finished food, data from our machines in the plant, local weather data and key attributes of raw materials, we used AI to create a 360-degree view of the production process for Krave,” says Reuben Calow, global VP for Kellanova’s work systems and digital supply chain.
We plan to scale AI across similar lines in the network in the next 12 months.
Reuben Calow, Kellanova
“Our front-line operators were critical to the pilot’s success. They were involved in developing our algorithms to ensure the tool’s assumptions reflected reality once deployed, making the tool stronger. In turn, AI helped our operators do their day-to-day work, armed with recommendations informed by real-time conditions and historic performance. Almost immediately, the tool started to help our operators achieve repeatable high-performance, reduce waste and predict the future.
“Before the pilot, we had a very efficient line, running with very little product lost to waste. However, after a year, the pilot project helped us realise €300,000 ($326,000) in annual savings by reducing our waste at start-up and ensuring that more product meets our high-quality standards for retail sale.”
Due to the “promising” results the company has achieved from the pilot projects Kellanova has already run, the company is weighing up where else in its network it could use AI, Calow says. “We plan to scale AI across similar lines in the network in the next 12 months based on these initial learnings.”
Danone has also been rolling AI out across its businesses globally over the past few years. The company already has 64 factories participating in its “digital manufacturing acceleration” programme and intends to roll the initiative out to up to 80 sites by the end of 2024.
In these factories, the French giant is using machine learning-based vision systems to detect production defects early, as well as machine learning-driven optical character recognition to process documents.
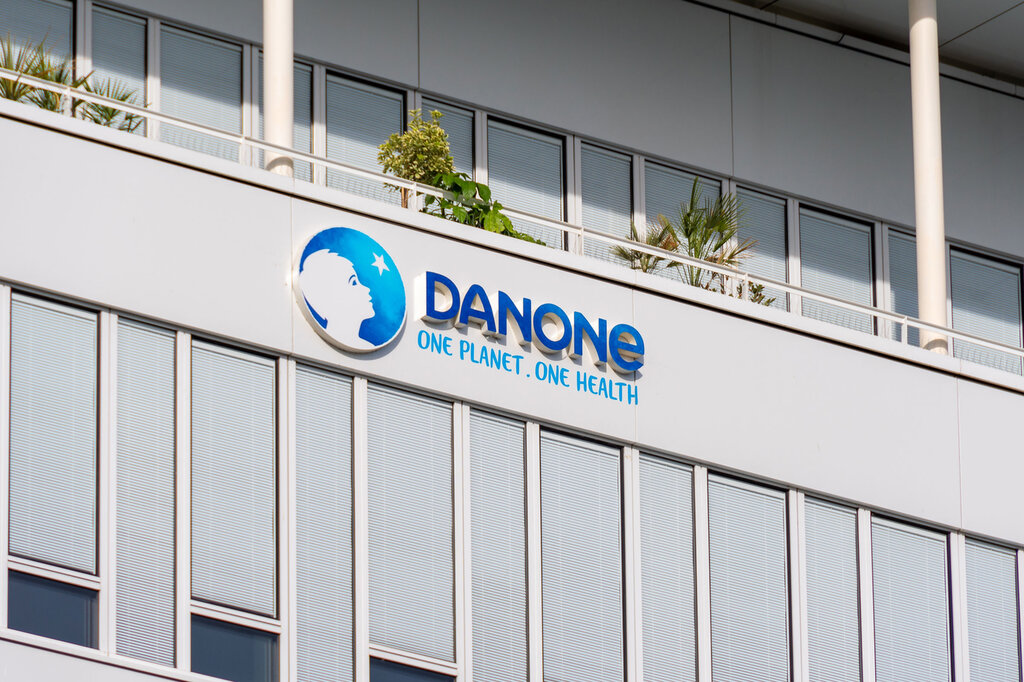
Credit: HJBC / Shutterstock.com
The Activia and Alpro owner, meanwhile, is using GenAI for data interaction and maintenance to ease the access to machine performance data on the shop floor.
“All of these tools collectively drive operational excellence and first-time right improvements across manufacturing and demonstrate how we are using digital alongside our people to both upskill them and empower them to support performance improvements within our factories,” explains Heiko Gerling, SVP for what Danone calls “global operations excellence”.
All of these tools collectively drive operational excellence.
Heiko Gerling, Danone
Gerling says the business is also using AI within planning. “By using advanced forecasting techniques such as AI together with leveraging large amounts and frequent data, Danone can sense the market signals more effectively and predict and plan for potential disruptions or events, while also positively contributing to reduce the environmental impact of our operations. Additionally, improved forecasting has helped us to more effectively manage inventory, reduce the risk of stockouts or overstocking, while also reducing waste and emissions related to inefficiencies.”
The issue of how the use of AI could affect human jobs remains a sensitive topic for businesses across industries. Gerling says the deployment of the technology means staff in planning roles can focus on “value-added” duties.
“Through the automatisation provided by AI, building the full forecast itself, demand planners save time and can focus on more productive value-added critical thinking tasks – i.e. increased collaboration with sales, marketing and finance teams, review portfolio performance, etc. – rather than creating the number itself.”
Another area of the business where the company has rolled out AI is sourcing and procurement. According to Jean-Yves Krummenacher, Danone’s SVP for procurement, the company is implementing AI tools that “empower procurement teams to make better and faster strategic sourcing decisions, optimising processes and enhancing overall performance”.
Krummenacher adds: “We deploy off-the-shelf AI software and have also developed in-house sourcing AI solutions, using our cloud-based data platform. These tools provide us with useful insights into the upstream supply chain risks, as well as help us make strategic sourcing decisions based on our products’ specifications.”
These examples scratch the surface and AlixPartners’ Agrawal believes that over the coming months and years we will see many more use cases of AI in the food sector emerging. Although he says some companies will inevitably be more reluctant to embrace the technology than others, one of the key upsides of AI is you can test and learn very quickly.
You don’t need to run multi-million-dollar, multi-year projects.
Abhinav Agrawal, AlixPartners
“You don’t need to run multi-million-dollar, multi-year projects,” says Agrawal. “You can run a project and in three months you can see the results. If it fails, you only spent three months on it and you can maybe learn from it, tweak your idea and adopt better.”
L2L’s Whitley agrees the ability to test and learn quickly is a major benefit of AI and he hopes that this will help businesses overcome any reservations they might have about rolling out the technology. Companies, he believes, can’t afford to delay implementing AI inside their manufacturing and supply-chain processes.
“If, in three or four years’ time, you’re only just popping your head out of the hole, you’re going to be so far behind that it could be detrimental to your business,” warns Whitley. “People need to be at least paying attention to the fact that this is something that’s happening now.”